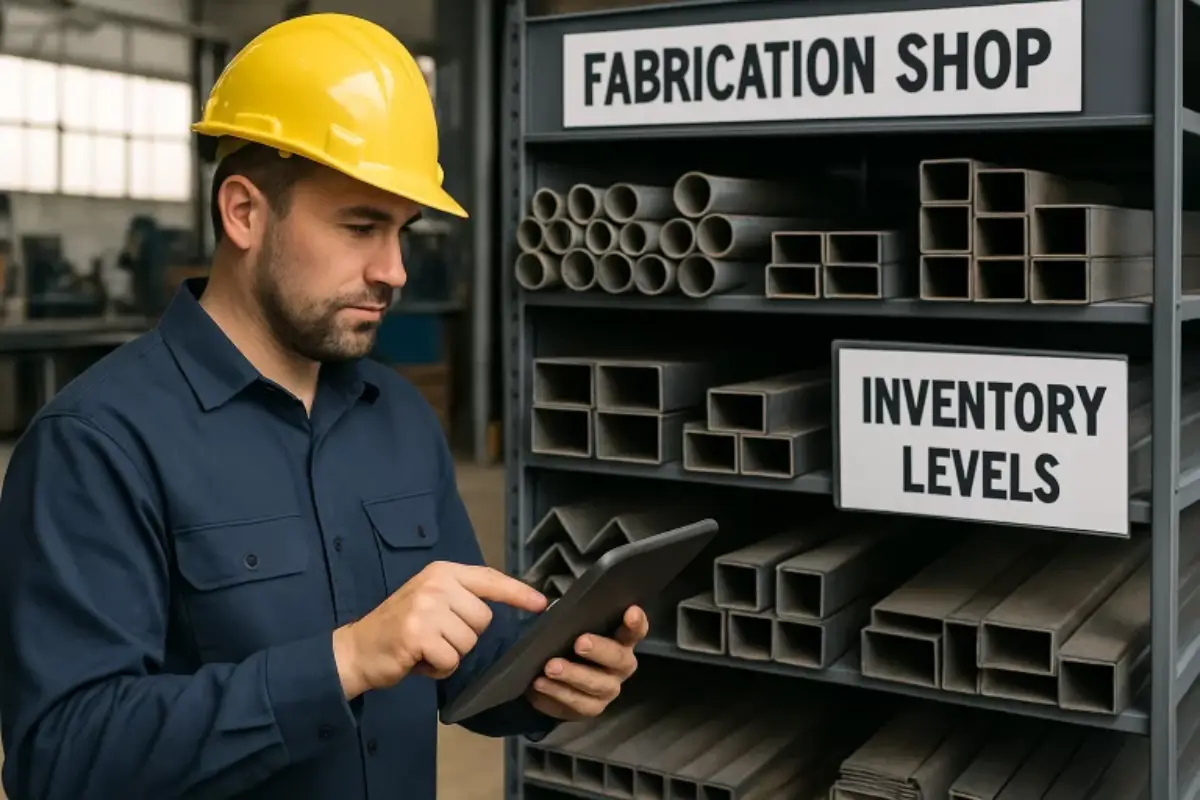
Transform Your Operations: How Fabrication Shop Management Software Can Enhance Business Growth
In today’s fiercely competitive metal fabrication industry, achieving operational efficiency and maintaining uncompromised precision can fuel significant business growth, profitability, and a positive industry reputation. Machine shop management software is designed to streamline and simplify the most complex aspects of shop operations, from intricate production workflows to critical data management.
By deploying sophisticated software tools, fabrication businesses can centralize key tasks—such as scheduling, quoting, invoicing, and communication—on a seamless, unified platform that provides actionable and real-time insights for more informed decision-making.
Implementing cloud-based fabrication shop management software represents a foundational shift, not just a replacement for paperwork, but an intelligent overhaul of how your business operates on a daily basis. This innovation brings together teams and data, connecting workflows like never before.
Such digital transformation serves as a springboard for automation, robust compliance, scalability, and future-proof growth, enabling fabricators to keep operating expenses in check, minimize costly mistakes, and consistently meet or exceed customer expectations. In a marketplace where speed and service quality make the difference, leveraging advanced technology translates into a vital competitive advantage and long-term business sustainability.
Contents
Streamlining Production Processes
A well-organized and agile production process is essential to success in metal fabrication. Fabrication shop management software enhances this process by automating tasks such as work order creation, resource allocation, and job tracking. It also uses intelligent algorithms to prevent bottlenecks, keep schedules on track, and alert teams to potential delays. This reduces time spent on manual coordination, allowing skilled staff to focus on innovation and problem-solving.
The software’s integrated dashboards improve visibility across production stages, reducing miscommunication. Features such as job prioritization and labor optimization can increase productivity by up to 25%.
Precise resource allocation ensures that machines, materials, and personnel operate efficiently together. As a result, plants experience faster turnaround times and improved responsiveness. Companies that utilize these systems gain a significant competitive advantage in capacity utilization.
Enhancing Inventory Management
Effective inventory management is crucial for profitability in fabrication, as stockouts and excess materials can harm margins and customer satisfaction. Fabrication shop management software helps prevent these issues with integrated inventory tools that offer complete visibility.
Managers can access real-time data on stock levels, reorder needs, and supplier lead times. This eliminates guesswork in restocking and improves planning accuracy. Additionally, all inventory transactions are automatically tracked, ensuring precise asset valuation and audit readiness.
The system utilizes analytics to forecast material needs based on job trends and demand projections. This enables the optimization of purchasing through bulk buying or just-in-time deliveries, thereby reducing waste and holding costs. Improved demand planning allows shops to manage inventory more effectively and avoid expensive last-minute orders.
Consequently, companies benefit from leaner inventory and more reliable project timelines. Businesses that utilize real-time inventory controls and forecasting often experience a revenue increase of 10% or more.
Improving Quoting and Estimating Accuracy
Manual quoting often leads to inconsistencies, delays, and inaccurate pricing, which can harm profitability. Shop management software eliminates this by using real-time data on material costs, labor rates, and machine availability to generate accurate quotes quickly. This minimizes human error and ensures pricing reflects actual project constraints.
Centralized version tracking further reduces disputes and rework by documenting every change in scope or cost, ensuring transparency and accuracy. Together, these tools enhance credibility, increase win rates, and build stronger customer trust.
Boosting Financial Management
Financial stability is crucial for daily operations and long-term growth in fabrication businesses. Integrated shop management platforms combine expense tracking, job costing, invoicing, and reporting into one system. This streamlines processes, eliminates double data entry, and improves overall financial accuracy.
Automated workflows reduce time spent on closing books, preparing taxes, and passing audits. As a result, shops often cut operational costs by up to 15% and make more informed financial decisions.
Enhancing Customer Satisfaction
Customer expectations are rising, and real-time project visibility helps meet them. Shop management systems provide clients with instant updates on order status, delivery timelines, and job progress. These platforms maintain consistent and clear communication, minimizing surprises and delays.
Fast response times and transparency encourage repeat business and positive word-of-mouth. In turn, this builds loyalty and helps shops establish a reputation as reliable, tech-driven partners.
Conclusion
Investing in fabrication shop management software creates measurable improvements across every department. It unifies quoting, inventory, production, accounting, and customer service into one streamlined system. This digital transformation boosts efficiency, reduces errors, and enhances responsiveness.
As a result, shops become more resilient and adaptable in a competitive industry. Ultimately, it positions businesses to capitalize on growth opportunities and thrive in the face of ongoing change.